Grinding equipment
Milling is one of the most important industrial processes. The electric power consumption by this process run on ore mining and processing enterprises is variously estimated as a value from 5 to 20% of overall world electric power. One of the major reasons of such a situation is the prevalence of conventional ball mills requiring large area and volume of industrial buildings and having low efficiency and specific capacity, high metal consumption as well as increased grinding bodies and linings consumption.
Crushing and milling Crushing and milling are usually classified according to the particle size of a crushed/milled product as follows: coarse crushing (300-100 mm), medium crushing (100-25 mm), fine crushing (25-1 mm); coarse grinding (1000-500 microns), medium grinding (500-100 microns), fine grinding (100-40 microns), and superfine grinding ( < 40 microns).
Crushing usually serves as pre-milling treatment and is intended for the production of a lumpy product having required lump size and granulometric composition. Milling is aimed to disaggregation, increase of the solid material surface area, attaining the necessary granulometric composition and particle shape. Milling facilitates: improvement of the mixture homogeneity, acceleration of heterogeneous chemical reactions and increase of their degree of conversion, increase of the intensity of various technological processes (mixing, drying, calcination and/or sintering, chemical reactions); decrease of temperatures and pressures applied; improvement of physico-chemical properties and structure of materials and articles manufactured (hard metals, concrete, ceramics, refractory materials); increase of the coloring power of pigments and colorants as well as adsorbent and catalyst activity; recycling of industrial wastes..
Milling can be undertaken in dry milling and wet milling modes. Dry milling is performed in air or in inert gas atmosphere (the latter is necessary for processing of oxidizable, inflammable, explosive and toxic materials). Before wet milling the treated material is mixed with liquid, mainly with water. Wet milling is applied in ore concentration and following treatment of suspended milled materials (for example in ТiO2 production), in the case of increased material moisture content, and if required to eliminate dust generation.
Milling can be performed in a batch or continuous way. Batch process is used on small industrial scale. Continuous process runs according to two main circuits. Open loop is often used for coarse and medium crushing. In the case of the open loop the material passes the milling device only once without repassing it. The best possible product quality level, the lowest power consumption, and the highest milling equipment output are achieved in closed loop with continuous recovery of the fine fraction. In such a loop the material having oversized particles is returned into the process chamber for regrinding and the target fraction is withdrawn during the following separation.
Crushing is performed mainly by crushers of the following types: jaw crushers, cone crushers, roll crushers, and impeller crushers. For example in impeller or hammer crushers the treated material is crushed by strokes of rotating swingingly mounted hammers or impact bars rigidly fixed on a rotor as well as by mutual collisions of material pieces and by their impacts against a stator or an impact plate surface.
There are various milling techniques. In the case of industrial milling equipment the following types of mechanical action are used: free stroke/impact, smashing, attrition and combinations thereof. The choice of loading depends on the material particle size and toughness.
Mills can be conveniently classified according to the shape and type of the active body into the following groups:
1) Drum mills including ball mills, rod mills, pebble mills, autogenous grinding mills;
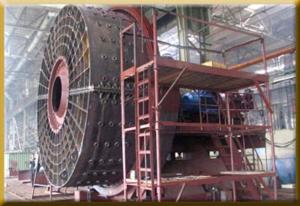 |
Cantilever-type mill for autogenous grinding (AG), semiautogenous grinding (SAG), and ball grinding MBK 5.0 – 1.1 (MK - 315), (TTD).
|
2) Roller mills: jar roller mills, ring mills, frictional-ball mills, runners /millstones;
3) Hammer mills, disintegrators;
4) Vibration mills /vibration grinding mills;
5) Jet mills, aerodynamic mills, mills without grinding bodies;
6) Attritors;
7) Planetary mills.
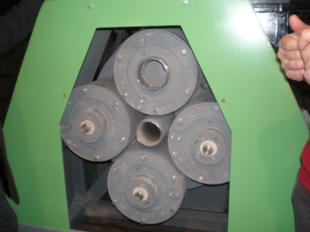 |
Batch-type planetary mill MPP-3 (TTD).
|
Since our company is concerned with superfine grinding and mechanical activation we are interested principally in planetary mills. Planetary mills possess high energy density allowing fast and efficient milling.
The energy density of milling equipment represents the quantity of mechanical energy transferred to the unit mass of the treated material in unit time
Table. Pressure acting on particles and energy density in milling equipment (data from the book by Chaikina M.V. “Mechanochemistry of natural and synthetic apatites”, Novosibirsk, Siberian Branch of the Russian Academy of Sciences, 2002, 220 pp.; in Russian)
Milling equipment
|
Pressure on particles, GPa
|
Energy density
|
Planetary mills |
3-8 |
High |
Attritors, vibration mills |
1-4 |
Medium |
Jet mills, disintegrators |
0,1-0,5 |
Low |
The following materials were used during construction of this web-page: Chemical encyclopedia. Pivnyak G.G., Vaisberg L.A., Kirichenko V.I., Pilov P.I. Kirichenko V.V. “Milling. Power engineering and technology”, work-book for higher education students; Moscow, “Ruda i Metally” publishing house, 2007, 296 pp.; in Russian.
|